Celebrating safety leadership in BC manufacturing
Kathy Sigstad2021-03-17T12:01:59-07:00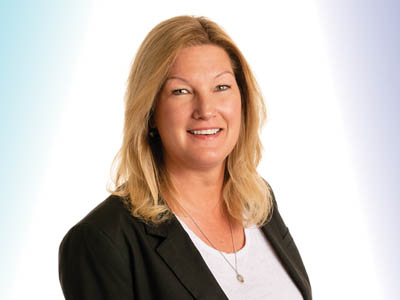
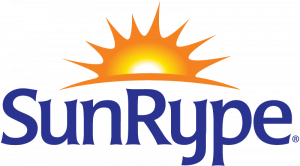
#safetyleader
Excellence in health and safety in the workplace starts at the top. In manufacturing, a leader’s commitment to safety helps establish the values, principles, and actions that create a safety culture.
In each edition of Make it Safe Magazine, we will feature a new #safetyleader. In this edition, we talked with Lesli Bradley, President and CEO of Sun-Rype Products and a member of the Alliance Board of Directors.
Lesli, what led you to make safety a commitment in your career?
Personally, for me, my safety journey started long before SunRype. While I have always been passionate about safety, unfortunately, a workplace accident early in my career imprinted on me how easily things can go wrong. My goal is to ensure everyone returns home at the end of a workday the same way they arrived, 100% of the time.
Who “owns” responsibility for safety in the workplace?
I wholeheartedly believe that safety is everyone’s responsibility. While management establishes policies, programs and procedures and needs to ensure employees are trained, educated, and comply with the requirements, every employee has responsibilities. As individuals as well as colleagues, we all have responsibilities for our actions and our safety.
How would you describe your approach to health and safety in your organization?
I believe my role is multifaceted when it comes to employee health and safety. My responsibility is to ensure the resources are available, be that human resources or financial resources, to ensure our programs and practices are not only compliant but exceed requirements. I also believe my role is to set the tone at the top. I need to consistently demonstrate and behave as I want others to do when it comes to safety. Not to overuse an old saying, but truly walking the talk.
What is your biggest safety challenge, and how do you work to overcome it?
Complacency is one of the biggest challenges we face when it comes to safety. We fight this challenge by ongoing observation and coaching. At SunRype, we believe observation and feedback processes do more than improve habits; it’s active encouragement of safety-related thinking—thinking about the job’s hazards and risks. We also incorporate safety in our daily tailgate and shift handoff meetings.
What is the role of leaders in fostering a culture of safety?
The role of the leader is to do just that, foster a culture of safety. It is essential that, as leaders, we do everything we can to ensure that safety is very high on the priority list regardless of who you are or where you work in the organization. The culture within a company is grown, not purchased or implemented, so ensuring that behaviours foster a safety culture is critical.
How do you create awareness about safety issues within your company?
We communicate about safety issues in several ways, including ensuring a cross-section of employees on the JHSC. Each department has a representative they can approach who is familiar with their area and can be a direct communication line. We also have shift tailgate and handoff meetings where two shifts can raise concerns and have a direct communication line with a supervisor.
What are you most proud of in regard to your safety program and approach?
My relationship with the Alliance is associated with SunRype’s continuous improvement safety journey. I joined SunRype 15 years ago, and at that time, we were introducing an abilities management program focusing on providing modified duties for employees. Next in our journey towards Zero lost-time accidents was a behaviour-based program, Safe Start, that our JHSC recommended. We have embraced this program and still use it today, ten years later.
The next goal in our journey to continuously improve was to strive to achieve OSSE certification. Over two years, SunRype worked towards that goal, and we have been certified since 2013. I genuinely believe achieving certification fundamentally influences an organization’s health and safety policies, practices, and focus.
Does a robust health and safety program support other aspects of your business?
Absolutely. In manufacturing, a safe work environment is critical to operations. Our safety program is the basis on which we build many programs, and they all mirror an objective of continuous improvement.
How do you define success for health and safety at your company? How do you measure safety?
We commit every year to meet and exceed requirements, and we strive for ZERO Lost time accidents. Our next steps are assessing our Culture within SunRype. We believe we have a culture grounded in safety and look forward to participating in the safety culture assessment.
Learn more about developing a healthy safety culture in your business: