Make it Safe Magazine
Kathy Sigstad2022-07-28T14:17:07-07:00The digital OHS magazine for manufacturers and food processors
In this issue
Editorial
OHS professionals need skills today to help protect workers from the risks of tomorrow
As leaders, we must help shape the professional standards, education, and credentialing of tomorrow’s OHS professionals so that they are equipped to tackle the health and safety challenges of the future.
Learn more about the Alliance’s five-year journey to research the labour market issues that have influenced the health and safety profession and how the resulting OHS Competency Framework will support companies to hire skilled practitioners to help employers created safe and healthy workplaces.
Health and safety for small businesses
Regardless of size – protecting workers on the job is the right thing to do
In a small business, an employer often wears many hats, and one of those hats is protecting their workers from injury and illness in the workplace. Employers, regardless of their size, are obligated to keep their workers safe.
“When you first decide to open a new business, you just don’t know that much about your obligations,” said Wayne Arondus, Chief Operations Officer at the Manufacturing Safety Alliance of BC. “You may not know, for example, that once you employ and pay workers – whether regular, casual or on contract – you must be registered and covered by WorkSafeBC.”
Congratulations 2021 Safety Excellence Award finalists
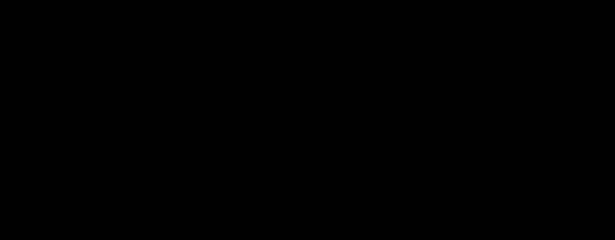
Register your team by July 31 to save 50% off the registration fee.
From labour shortages to supply disruptions, automation to hybrid work environments, the decisions facing industry today are impacting your people’s health, safety, and performance. It’s time to reset. Learn from industry leaders, global experts, and peers at Make It Safe 2021.
Get new perspectives and learn from the experience of industry leaders and health and safety experts at Make It Safe 2021.
Your 2 cents: Why we need to hear from health and safety experts
Disability management can be very complex; balancing effective administration and planning, while compassionately handling the human elements of return-to-work is certainly a challenge.
TeksMed Services Inc. recognizes that the difficulties that come with trying to manage both health and safety as well as injury and claim management are often insurmountable with internal resources alone.
In an effort to best support the health and safety professionals in the manufacturing industry, we are looking for feedback from authorities in the field – those immersed in the world of health and safety. We want to know the specific challenges you are facing, to best support the manufacturing health and safety specialists such as yourself. We understand that the work environments and nature of the industry bring unique challenges and needs when it comes to disability management.
We need your help so that we can best serve those who are struggling with – or are looking to enhance – their current disability management program.
TeksMed wants to collect responses from you, the experts with first hand experience in health and safety within the manufacturing industry.
Once you complete the following questions, visit us at the Make it Safe conference in October and we’ll have a gift to thank you for participating!
The level of professional commitment offered by the Alliance staff is outstanding. The immediacy, and the depth of their reply to any inquiry I've ever made has been excellent—always!
Upcoming training and events
Upcoming virtual open learning classes
Aug 5 | Fundamentals of Thermal Imaging
Sep 8 | Hazard ID and Control
Sep 8| Joint Health and Safety Committee
Sep 22 | Workplace Inspections
Make it Safe Conference + Trade Show
October 28 / 29
At Make It Safe 2021, join industry experts – in Canada and around the world – to consider the challenges we face today across all industries and learn new strategies to assess the risk. Recognize where business, environment, people, and safety intersect, and discover new approaches and controls.
Register your team now for Super Early Bird savings!
Partnership opportunities are also available for Make It Safe. Join us as a sponsor or exhibitor to connect with manufacturing leaders and influencers.
OSSE internal auditor training
Sept 22 | 8:30 am – 5 pm
This training course is for OSSE-certified companies (large employers) that must have an employee trained as an internal auditor to perform a maintenance audit in 2021.
NEW online course
Emergency Response Awareness
Online course | $49
Emergency Response Awareness explores different types of emergency situations that you may encounter in manufacturing.
Expand your understanding of emergency response with this online course. This self-paced course takes about 90 minutes and can be completed at your own pace.
OHS Training Bundle
Hazard ID + Workplace Inspections + Incident Investigations | $135
SAVE when you purchase three of our most popular online safety training courses together: The OHS Basics Bundle gets you Hazard ID, Incident Investigation, and Workplace Inspections in one convenient package.
Emergency response planning
Why planning for a “someday situation” better equips you to tackle challenges today
Earthquakes, forest fires, flooding, and viral outbreaks are just a few of the potential emergency scenarios we face in British Columbia.
While some companies have crafted and rehearsed plans to address emergencies such as these, many in the past two years were forced to build a response plan on the fly in the highly charged early days of the pandemic.
You did it. Your team rose to the challenge. But what toll did it take on your people and your business in those challenging first weeks?
3 tips
3 tips to beat the summer heat
Heat-related illnesses happen when a person heats up faster than they can cool down. Heat stress ranges from mild to severe – and heat stroke can be deadly when it’s not caught early and treated. Heat-related illness IS preventable with the right preparation.
1
Employers can prepare ahead of hot days to protect workers from the impacts of working in the heat. Be aware of changes in the weather that could create issues for employees working outside or in hot environments. Mitigate the heat by providing places to cool down, adequate water and hydration breaks throughout the day, sun protection, and increased check-ins with workers to monitor for the signs of heat-related illness.
2
Make workers aware of the signs of heat-related illness and ask them to watch for any early symptoms in themselves and their co-workers. Early signs of heat stress include headache, dizziness or confusion, heavy sweating, cool, pale, and damp skin, nausea or vomiting, and tiredness or weakness. Heat stress can rapidly progress to heat stroke — which is a medical emergency.
3
Ensure that first aiders are aware of the symptoms of heat-related illness and the protocols to treat it. Now is a great opportunity to review your inventory of first aid supplies as well. Heat stress can be treated by moving the worker to a cooled space, spraying with cold water or providing a cool shower, removing excess clothing, and placing cool, wet towels or ice packs on the neck, armpits, and groin.
If signs suggest that your worker is experiencing heat stroke, call 9-1-1 immediately. Heat stroke is a potentially life-threatening condition that requires medical attention.
Gate Gourmet's long-term commitment to certification
Staying the course
For Gate Gourmet, OSSE certification has been much more than a one-time accomplishment — it has become part of the way they manage their business.
Learn how achieving and maintaining the Occupational Safety Standard of Excellence has positively influenced their culture, engagement, recruitment, and retention.
Take control of your team’s training
Is your company looking for a way to streamline training for your organization? A customized company learning portal may be the answer.
- Enroll staff instantly in the training they need
- Access training anytime, anywhere
- Supervise, track and report your employee’s learning progress
- Real time data access
- Multi-language support
- Reduce overhead and save time in training admin
#safetyleader
Alliance Board of Directors changes
Serving on a board of directors is a notable commitment. Volunteer board members take time out of their busy professional and personal lives to fill this vital role. We are enormously grateful to the dedicated professionals who have committed to protecting the health and safety of BC manufacturing workers by serving as members of our Board of Directors.
In June, our Annual General Meeting marked the departure of two long-standing Board members—Jason Longden and Kevin Thorburn.
Kevin Thorburn, a senior project engineering manager with Nestlé Canada, served the maximum tenure of six years as a Board member.
Jason Longden, CEO at Fine Choice Foods, also served a complete tenure and then returned to take on the role of Chair during what would prove to be a challenging year.
“I’d already served my six years on the board in April 2020 when I was asked to take on the role of Chair after the previous Chair relocated to the UK,” recalls Jason. “When Lisa asked me to take on the role of Board Chair, it allowed me to help the Alliance craft their approach to COVID-19.”
Jason retired from the Board at the AGM and was succeeded as Chair by Nick Reiach, Senior Leader at Tupper Street Consulting.
Lesli Bradley, President and CEO of Sun-Rype Products, joins Nick as the Vice-Chair. Nick and Lesli are both returning Board members.
Members also elected four new Directors in early June. We are grateful for the expert guidance of new board members:
Amit Golan, Plant Manager, CKF Inc.
Andy McEachern, Senior Vice-President, Peerless
Vince Sciamanna, President, The Garaventa Lift Group
Garnet Zimmerman, Principal, GZ Mediation Inc.